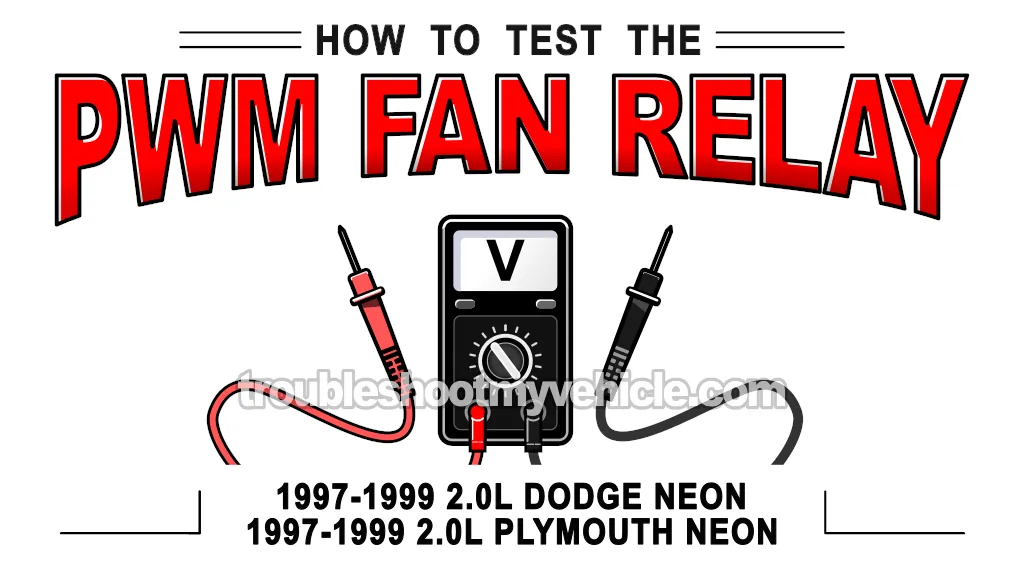
Diagnosing the PWM fan relay in the 1997-1999 Neon as good or bad isn't a difficult. In this tutorial, I'll guide you through a straightforward testing process that I use to determine its condition. By the end of this tutorial, your test results will let you know whether the PWM fan relay is functioning properly or not.
It's important to note that the PWM fan relay cannot be directly tested using a standard multimeter resistance test. Instead, it requires a dynamic test — meaning it has to be tested while it's in operation, and that's exactly what I'm going to show you.
Also, you won't need a scan tool for this tutorial, and it doesn't matter whether the AC system in your Dodge/Plymouth Neon is working or not.
Content of this tutorial:
- Symptoms Of A Bad PWM Fan Relay.
- PWM Fan Relay Basics.
- Why Does The PWM Relay Fail So Much?
- PWM Fan Relay Connector Circuits.
- TEST 1: Checking The Radiator Fan Motor Circuit Diode.
- TEST 2: Making Sure That Terminal 4 Of The PWM Fan Relay Connector Has 12 Volts.
- TEST 3: Making Sure That Terminal 1 Of The PWM Fan Relay Connector Has Ground.
- TEST 4: Manually Activating The PWM Fan Relay (Fan Motors Connected).
- TEST 5: Manually Activating The PWM Fan Relay (Fan Motors Disconnected).
You can find this tutorial in Spanish here: Cómo Probar El Relé PWM Del Ventilador Del Radiador (1997-1999 2.0L SOHC Dodge/Plymouth Neon) (at: autotecnico-online.com).
APPLIES TO: This tutorial applies to the following vehicles:
- 2.0L Dodge Neon: 1997, 1998, 1999.
- 2.0L Plymouth Neon: 1997, 1998, 1999.
Symptoms Of A Bad PWM Fan Relay
The PWM fan relay plays a central role in activating the radiator fan or fan motors. Here are the key symptoms to look out for when it fails:
- Overheating Engine: The most noticeable symptom is engine overheating, especially during idling or low-speed driving. Since the radiator fan helps to cool the engine by drawing air through the radiator, a non-functional fan due to a failed relay will cause the engine to overheat.
- No Radiator Fan Activation: You'll notice that the radiator fan doesn't run at all. Normally, the fan should activate when the engine reaches a certain temperature or when the air conditioning is running. If the fan or fans don't turn on in these conditions, it could be due to a bad PWM relay.
- Air Conditioning Problems: Since the radiator fan also helps in cooling the refrigerant for the air conditioning system, a faulty fan relay can affect the AC's performance. You might notice that the AC isn't cooling as effectively as it should.
- Check Engine Light or Error Codes: In some cases, the car's onboard diagnostic system may detect the PWM fan relay problem and illuminate the Check Engine Light.
- Intermittent Fan Operation: Sometimes, a failing PWM fan relay can cause the radiator fan to operate intermittently. The fan may randomly start and stop or work at lower speeds than necessary, which doesn't provide enough cooling effect to keep the engine cool.
PWM Fan Relay Basics
The PWM (Pulse Width Modulation) fan relay in the 1997-1999 2.0L Dodge Neon is part of a more sophisticated cooling system control compared to the older, simpler mechanical on/off relay system used on the 1995-1996 Neons. Here's a basic overview of how it works:
PWM Fan Relay Function
- Variable Speed Control: Unlike traditional relays that simply turn the fan on or off, the PWM relay can vary the speed of the fan. This is achieved by sending pulses of varying width to the fan motor, which in turn controls how fast the fan spins.
- Pulse Width Modulation: The term "Pulse Width Modulation" refers to the technique of modifying the width of the control signal pulses sent to the fan motor relay. By adjusting the duration of these pulses (the "width"), the Powertrain Control Module (PCM) can precisely control the fan's speed through the PWM fan relay.
- Cooling Efficiency: This allows for more efficient cooling, as the fan can run at lower speeds when less cooling is needed, reducing noise and energy consumption.
Activation by the PCM:
- Engine Coolant Temperature (ECT) Sensor: The PCM receives data from the ECT sensor and other sensors. These sensors inform the PCM about the current operating conditions of the engine.
- PCM Processing: Based on this input, the PCM determines the required cooling level. If the engine temperature is rising and needs more cooling, the PCM will decide to increase the fan speed.
- Signal to PWM Relay: The PCM sends a signal to the PWM relay, adjusting the pulse width. A wider pulse means higher voltage and thus higher fan speed, and a narrower pulse results in lower speed.
- Feedback Loop: The PCM continuously monitors engine conditions and adjusts the fan speed accordingly. This feedback loop allows for dynamic adjustment of cooling based on real-time engine needs.
Why Does The PWM Relay Fail So Much?
The PWM fan relay in the Neon is infamous for how easily it fails (it's a known money-maker, the epitome of the gift that keeps on giving to the patent holder, the dealer, the independent repair shop, the auto parts store, ...).
It fails primarily due to two interrelated factors: heat stress and increased amperage draw from the fan motor or motors (when they fail). Here's a breakdown of why this happens:
- Heat Stress: The PWM relay naturally generates a lot of heat while the fan motor or motors are running. This heat is a result of the electrical current flowing through its electronic components and to the fan motor(s). Over time, this heat will degrade the relay's electronic components, eventually leading to their failure, and consequently, the failure of the relay.
- Increased Amperage Draw from the Fan Motor: As the radiator fan motor ages or becomes faulty, it starts requiring more current to function. This higher amperage draw leads to additional heat generation within the PWM relay. Since the relay in the Neon is not designed to handle amperage draws of 30 Amps or more, this increased load exacerbates the heat issue and fries the relay's internal electronic components. A bad fan motor using with an amperage draw of 30 or Amps is the number 1 killer of PWM fan relays.
- Inadequate Heat Dissipation: The design of the PWM relay really doesn't effectively dissipate the heat it generates. I mean, it probably should have it's own cooling fan! Over time, this design flaw will cause the internal components to fail, especially under the stress of a high current draw from a failing fan motor or motors.
- Connector Issues: An often-overlooked factor is the PWM relay's connector. The intense heat from the relay, which is caused from a bad fan motor's higher-than-normal amperage draw, can lead to the connector melting. Once the connector has melted, the tight fit of the female terminals on the relay's male terminals is lost. When the new relay is installed, the damaged connector will now contribute to its failure.
PWM Fan Relay Connector Circuits
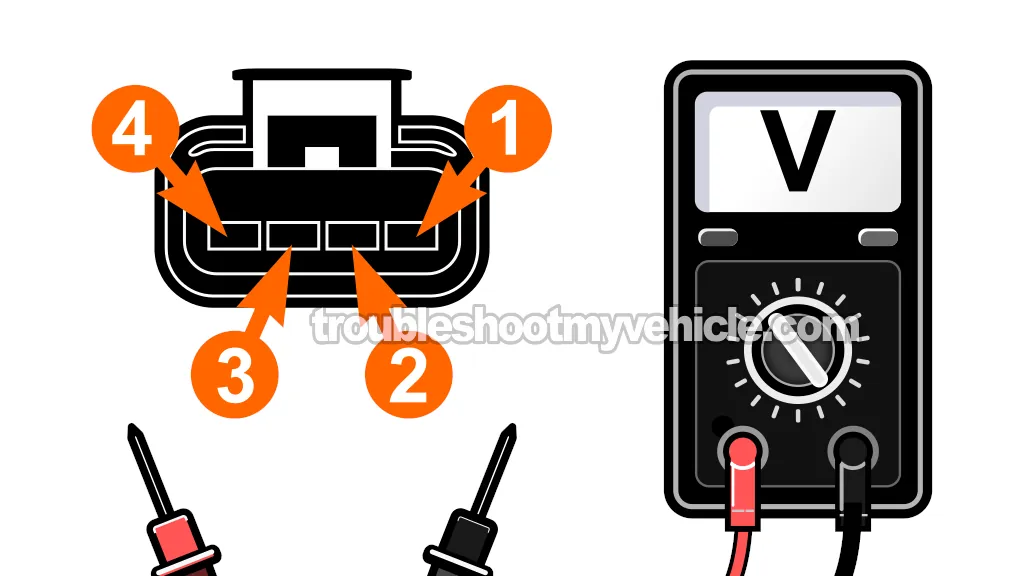
The illustration of the PWM fan relay connector is a front view of the connector (female terminal view). The connector has four wires coming out of it. Here's a description of each:
Wire | Color | Description |
---|---|---|
1 | Black (BLK) | Ground |
2 | Dark Green (DK GRN) | Radiator Fan Relay Control PWM Signal |
3 | Light green (LT GRN) | Radiator Fan Relay Output To Fan Motor Or Motors |
4 | Grey (GRY) | 12 Volts (from fuse #11 Power Distribution Center) |
LOCATION OF PWM FAN RELAY: The radiator fan relay is located in the engine compartment, near the driver's side front wheel well. It's mounted with two small bolts to the inner side of the left frame rail under the battery.
Fuse #11 is a 30 Amps fuse and located in the Power Distribution Center. You can find a complete listing of the locations and descriptions of the fuses and relays of the Power Distribution Center here:
TEST 1: Checking The Radiator Fan Motor Circuit's Diode
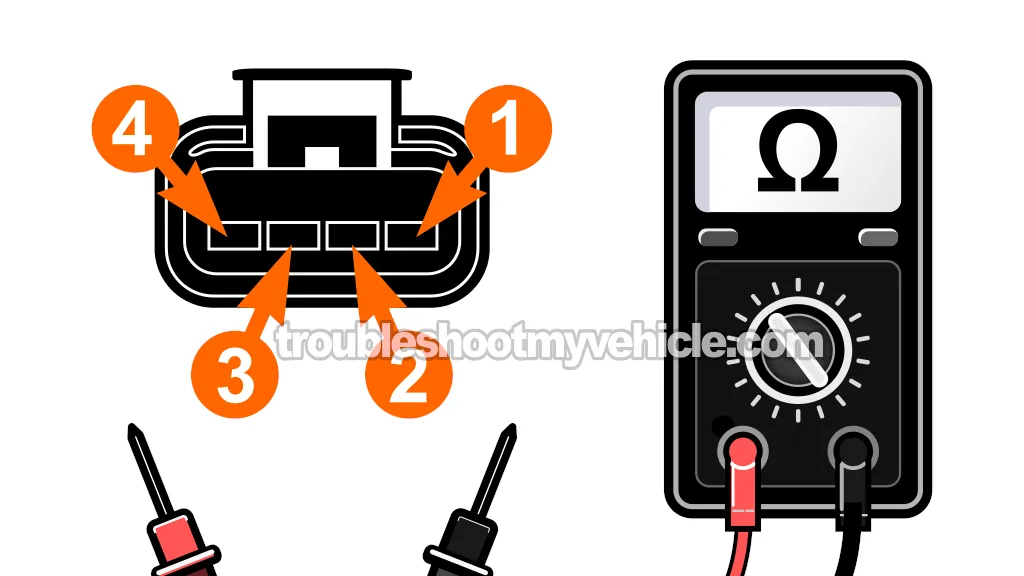
The first thing that we're gonna do is check the condition of the diode that protects the fan motor circuit. To get the most accurate test result, we'll need to isolate the diode.
We can easily isolate the diode by disconnecting PWM fan relay and the fan motor or fan motors (dual fan motor setup) from their connectors (no need to yank it out of the engine wiring harness).
In all of the single fan motor systems (and in a few dual fan motor setups), you'll need to disconnect the connector that is directly attached to the fan motor body. We'll call this specific connector the 'primary connector'.
In the majority of the Neon dual fan motor systems, it's not uncommon to find that one of the fan motor assemblies doesn't have a primary connector attached to its body, while the other has one. Also, you'll notice that the two wires from each of the fan motors converge into a single connector, which then connects to the engine wiring harness's single-point connector.
In these dual fan systems, there's no need to disconnect the primary connector from either fan motor (after all, one of them doesn't have one). Instead, simply disconnect the single-point connector from the engine wiring harness. This effectively disconnects both fan motors and you're good to go.
CAUTION: The diode test is done by probing certain terminals on the PWM fan relay connector. There's a good chance that the metal test lead tips of the multimeter might be too wide to probe the female terminals of the connector. To avoid damaging these terminals, consider using a thinner probe attachment. This will help you make contact with the metal terminals without damaging the connector or its terminals.
Let's get going:
- 1
Disconnect the negative (-) battery cable from the negative (-) battery post.
- 2
Disconnect the PWM fan relay from its 4-wire connector.
- 3
Disconnect the fan motor or fan motors from their electrical connectors.
Single fan setup: The connector you'll need to disconnect is the one that connects directly on the fan motor's metal body.
Dual fan setup: Disconnect the single point connector that connects to the engine wiring harness. - 4
Set your multimeter to Ohms (Ω) mode.
- 5
RESISTANCE TEST 1 OF 2 (Forward Biased):
A.) Connect the red multimeter test lead to terminal number 1 of the PWM fan relay.
B.) Connect the black multimeter test lead to terminal number 3 of the PWM fan relay.
C.) Your multimeter should show continuity (report about 1 KΩ to 10 MΩ). - 6
RESISTANCE TEST 2 OF 2 (Reversed Biased):
A.) Connect the red multimeter test lead to terminal number 3 of the PWM fan relay.
B.) Connect the black multimeter test lead to terminal number 1 of the PWM fan relay.
C.) Your multimeter should report no continuity and display OL (over limit). - 7
Reconnect the battery negative (-) cable to the battery.
Let's interpret your test result:
CASE 1: The multimeter showed continuity in one direction (forward biased) and OL in the opposite direction (reverse biased). So far so good, as this is the correct and expected test result.
Your next step is to go to: TEST 2: Making Sure That Terminal 4 Of The PWM Fan Relay Connector Has 12 Volts.
CASE 2: The multimeter showed the same readings in both directions. This test result tells you that the fan motor circuit diode is bad.
Although it's beyond the scope of this tutorial to replace the fan motor circuit diode, your next step is to replace it.