TEST 3: Checking The IAC Valve Wires For A Short To Ground
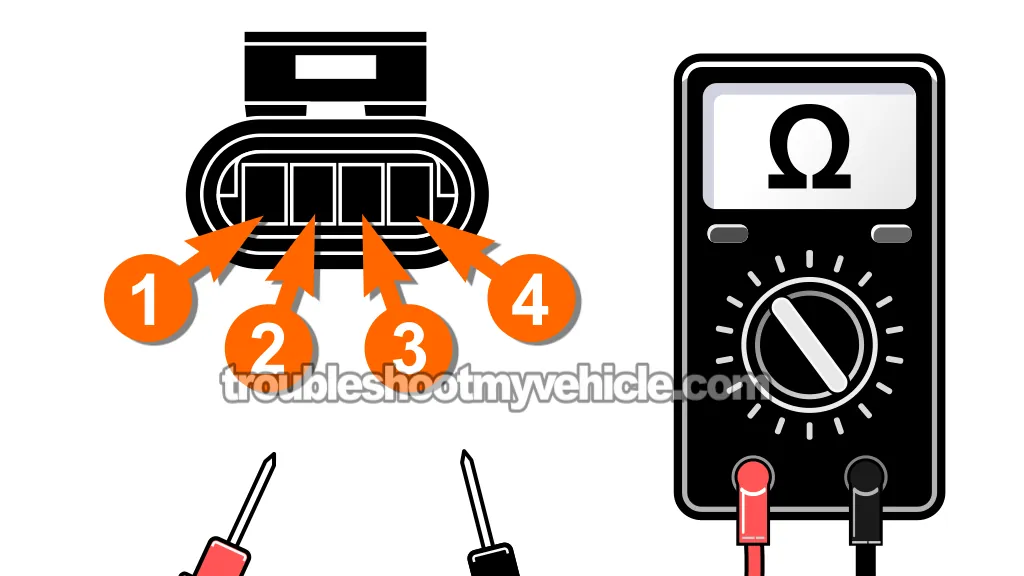
This test checks if any of the IAC valve wires are shorted directly to Ground. Like in TEST 2, each wire at the IAC connector should be electrically separate —not just from the others, but also from Ground.
A short to Ground can occur when a wire's insulation gets worn down or damaged, exposing the copper inside. If that bare wire makes contact with the engine block or any Grounded metal part, it'll disrupt the FI computer's ability to control the IAC valve.
When that happens, you'll almost certainly get a Code 25: Idle Air Control (IAC) Circuit.
IMPORTANT: Make sure the negative battery cable is disconnected from the battery terminal before running this test. That prevents the battery from affecting your readings.
OK, let's get started checking for a short to Ground:
- 1
Disconnect the negative (-) battery cable from the battery.
You'll use the cable end as your Ground reference for this test. - 2
Unplug both the IAC valve connector and the FI computer connector.
NOTE: This makes sure you're only testing the wiring —with no interference from the IAC valve or FI computer. - 3
Switch your multimeter to its Ohms (Ω) setting.
IMPORTANT: Avoid using the continuity (beep) function —it's not as precise for this test. - 4
Connect one lead of your multimeter to Terminal 1 at the IAC connector. Touch the other lead to the loose battery negative (-) cable (your Ground point).
- 5
Look for continuity on the meter.
- 6
You should see infinite resistance (no continuity).
If the meter shows a low resistance reading (5 Ohms or less), that wire is Grounded somewhere it shouldn't be. - 7
Repeat this check on Terminals 2, 3, and 4, always testing each one against Ground individually.
- 8
Have a helper gently move and wiggle the engine wiring harness while you monitor the multimeter.
Focus on areas between the IAC connector and PCM connector —especially spots with sharp bends, or where the harness could possible rub against a bracket or a sharp edged engine part. - 9
Keep an eye out for sudden changes in resistance as your helper wiggles the engine wiring harness.
If the reading drops sharply —say to 5 Ohms or less— that's a classic sign of an intermittent short inside the harness.
Here's how to interpret the results:
CASE 1: No continuity —infinite resistance on all four terminals. That's what you want. None of the IAC wires are Grounded, so the circuits are in good shape.
Go ahead and continue to: TEST 4: Check IAC Valve Stepper Motor Resistance (From FI computer Connector).
CASE 2: Continuity detected —low resistance on one or more terminals. This indicates one or more wires are shorted to Ground between the IAC connector and the FI computer.
Inspect the harness closely, especially in areas where the wiring might rub against metal brackets, sharp edges, or hot engine parts. Fix or replace any damaged sections. For repair guidelines, see: How To Repair Shorted IAC Wires (Real-World Fix).
TEST 4: Checking The IAC Valve Stepper Motor Resistance (From FI Computer Connector)
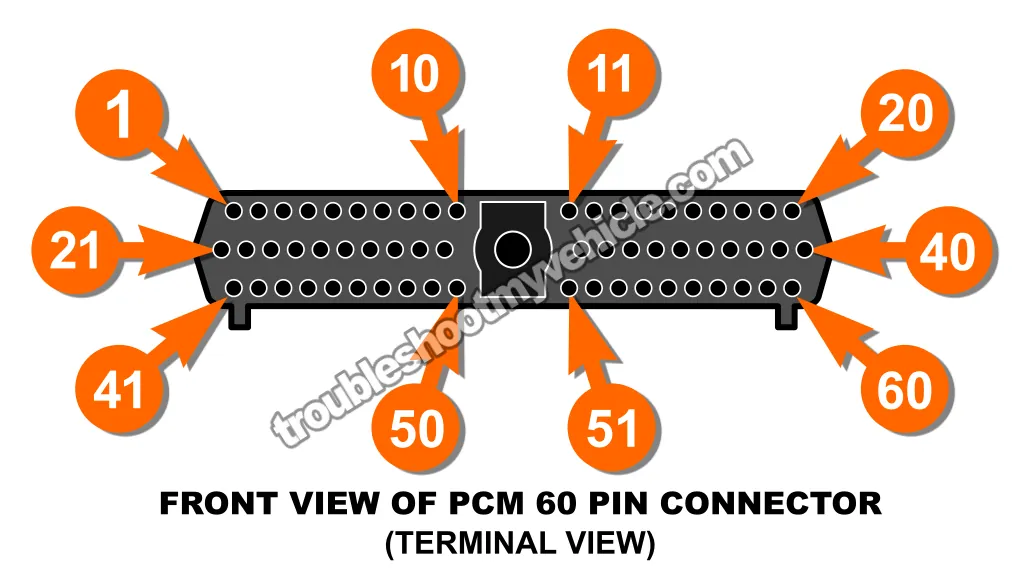
At this stage, you've already ruled out common wiring issues:
- The connector and its 4 wires are OK (TEST 1).
- No shorts between IAC circuits (TEST 2).
- No shorts to Ground (TEST 3).
Now it's time to check the condition of the IAC valve itself —specifically, the two internal stepper motors that move the pintle back and forth.
Each motor is controlled by a pair of wires that run straight to the FI computer. In this test, we'll measure the resistance between the appropriate terminals at the FI computer connector to evaluate each motor.
On a working IAC valve, resistance should read close to 35 Ohms for each motor (some have reported 8 to 10 Ohms). This isn't an official factory spec, but it's the typical range you'll see on a good, functioning valve.
The important thing is that both motors show similar resistance values. If one reading is way off —or if the meter shows an open-circuit (infinite resistance) or a dead short (very low resistance)— then the motor is bad and the IAC valve needs replacing.
IMPORTANT WARNING: Be very careful when probing the the round female terminals of the computer's 60 pin connector. Do not jam regular multimeter leads into them —they're often too thick and can damage or deform the terminals permanently. This kind of damage can lead to poor contact, strange engine behavior, or total failure of the circuit. Always use the appropriate probe designed for terminal testing. Handle this step with great care.
Alright, let's check the resistance of the IAC valve's stepper motors:
- 1
Double-check that the battery's negative (-) cable is still disconnected.
- 2
Disconnect the FI computer from its 60 pin connector.
- 3
Plug the IAC valve back into its 4-wire connector.
- 4
Set your multimeter to measure resistance (Ohms, Ω).
- 5
To check Stepper Motor 1:
Place the multimeter leads on FI computer connector terminals 39 and 60.
You should get a reading close to 35 Ohms (some folks report 8 to 10 Ohms). - 6
To check Stepper Motor 2:
Now measure between FI computer terminals 40 and 59.
Expect a similar resistance —around 35 Ohms (some folks report 8 to 10 Ohms). - 7
The resistance values of both stepper motors should be almost identical.
If either reading shows no continuity (infinite resistance) or very low resistance (close to zero), that means one of the internal coils is bad —and the IAC valve will need to be replaced.
Here's how to read your results:
CASE 1: Both measurements are close to 35 Ohms. Perfect. The stepper motor windings are intact. If you're still having issues, it might be due to carbon buildup or a sticking pintle inside the valve. For more, see: What If The PCM Itself Is Bad?
CASE 2: One or both tests show infinite resistance. This points to a broken coil inside the valve —an open-circuit. Time to replace the IAC valve.
CASE 3: One or both tests show near-zero resistance. That means there's a shorted coil inside the valve. It can't function correctly and should be replaced.
What If The PCM Itself Is Bad?
A faulty FI computer —specifically, a failure in the internal IAC driver circuits —can sometimes be the cause of a Code 25. But let's be clear: this is very uncommon.
The tricky part is that there's no way to test the FI computer's IAC driver circuits directly with a multimeter or scan tool.
These circuits are solid-state components sealed inside the computer. If one fails, the computer may stop sending the right signals to the IAC valve, which can lead to stalling, rough or high idle, and eventually trigger a Code 25.
That said, a bad FI computer should only be considered a last resort —after every other possibility has been checked and ruled out.
Make sure all of the following have passed inspection first:
- No IAC valve wires are shorted to Ground or to each other.
- Both IAC valve stepper motors show good resistance.
- The IAC valve connector is undamaged, clean, tight, and its metal terminals are free of corrosion.
- The intake manifold gasket is sealing properly.
- No vacuum leaks near the throttle body.
- Both throttle plates and their bores (in the throttle body) are in good shape and not sticking.
- The idle stop screw hasn't been adjusted or tampered with.
If all of these areas check out and you're still dealing with idle issues and a recurring Code 25, then —and only then— it may point to an internal FI computer fault.
The only reliable way to confirm this is by installing a known-good FI computer and observing whether the problem disappears. If it does, you've found your answer.
Still, it's worth repeating: FI computer failure is rare. So always start with wiring, mechanical issues, and the IAC valve itself before pointing fingers at the computer.
How To Repair Shorted IAC Wires (Real-World Fix)
If you've confirmed that two IAC wires are shorted together —and the damaged section is buried somewhere inside the wiring harness where you can't easily see or reach it— don't worry.
You don't need to cut open the entire harness and trace every inch of wire. That's usually not how it's done in a real-world repair scenario.
Instead, the go-to solution is to bypass the bad section altogether by splicing in a new wire. It's simple, effective, and holds up long-term when done right.
Here's how to do it:
- Snip the problem wire(s) at least 3 to 4 inches away from the IAC connector to ensure you're past the damaged area.
- Do the same near the FI computer connector —cut into a clean section of wire with no visible damage.
- Use new wire with the same thickness (gauge) and insulation type. Strip both ends and solder the new wire in place.
- Avoid using butt connectors. While they might work at first, they're prone to loosening over time due to vibration or movement, which can lead to connection issues down the road.
- After soldering, protect the repair with heat shrink tubing or high-grade electrical tape to seal out moisture and provide long-lasting durability.
While replacing the entire engine harness is technically the ideal repair, it's rarely necessary. A proper splice like this will generally work without any further issues and can be considered a permanent, professional fix.
More 5.2L, 5.9L V8 Dodge Ram Pickup Tutorials
I've written several more tutorials for the V8 Dodge Ram pickups that may be of interest to you that you can find in this index:
Here's a sample of the tutorials you'll find in the index:
- How To Test The Fuel Pump (1992-2003 5.2L, 5.9L V8 Dodge Ram Pickup).
- How To Test The Intake Air Temp (IAT) Sensor (1998-2003 5.2L, 5.9L V8 Dodge Ram Pickup).
- How To Test The Camshaft Position Sensor (1998-2003 5.2L, 5.9L V8 Dodge Ram Pickup).
- Troubleshooting A Blown Head Gasket (1989-2003 5.2L, 5.9L V8 Dodge Ram Pickup).
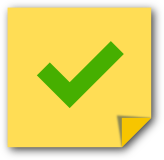
If this info saved the day, buy me a beer!
