TEST 3: Fuel Injector Resistance Test
NOTE: This test is only for when one injector is spraying fuel and the other one isn't.
It's pretty common for fuel injectors to wear out over time. When that happens, the internal windings can either suffer an open-circuit or short-circuit failure.
- Open-circuit failure: Your multimeter will show infinite resistance. On a digital meter, that usually means you'll see OL (Over Limit).
- Short-circuit failure: The resistance will read really low —usually between 0 and 1 Ohm.
The way to be sure is by measuring the injector's internal resistance. With the engine completely cold (this is important), the reading should land somewhere between 10 and 16 Ohms.
Since in TEST 1 you saw one injector working and the other one dead, you'll want to compare their resistance readings. The one that isn't spraying should read almost the same as the working one. If it doesn't, that non-spraying injector is the one that's bad.
NOTE: Don't have a multimeter or need to upgrade yours? This is the one I use and recommend: Tekpower TP8268 AC/DC Auto/Manual Range Digital Multimeter (at: amazon.com).
IMPORTANT: We're gonna check the resistance at the 4-wire connector for the fuel injectors —we're not popping off the injector caps to get to the terminals directly. That said, if you'd rather measure resistance right at the injectors, you can remove the caps and do it that way too.
Alright, here's how:
- 1
Unplug the 4-wire connector going to the fuel injectors.
- 2
Set your multimeter to measure Ohms (resistance).
- 3
Check resistance between terminals 1 and 2 (male pins). Use the photo above to find the correct pins.
NOTE: You're testing between the round male pins on the injector-side connector —not the round female terminals from the wiring harness side. - 4
You should get a reading between 10 and 16 Ohms.
- 5
Now test between terminals 3 and 4.
- 6
You should see between 10 and 16 Ohms again.
Here's how to make sense of your readings:
CASE 1: Both injectors show similar resistance in the 10–16 Ohm range. That's a good sign —it means the non-spraying injector isn't damaged internally.
Even though the electrical side checks out, we've still gotta make sure it's getting power. Next step: TEST 5: Making Sure The Fuel Injector Is Getting Power.
CASE 2: The injector that's not working shows a resistance reading that's out of range. Go ahead and retest it to double-check.
If it's still reading wrong —and it's way off compared to the working injector— here's what to do next:
- Take off the plastic hold-down caps on both injectors.
- Measure resistance directly on the injector terminals themselves.
If that non-spraying injector still gives you a bad reading —or it's way off compared to the good one —then it's done for and needs to be replaced.
TEST 4: Fuel Injector Activation Signal Test
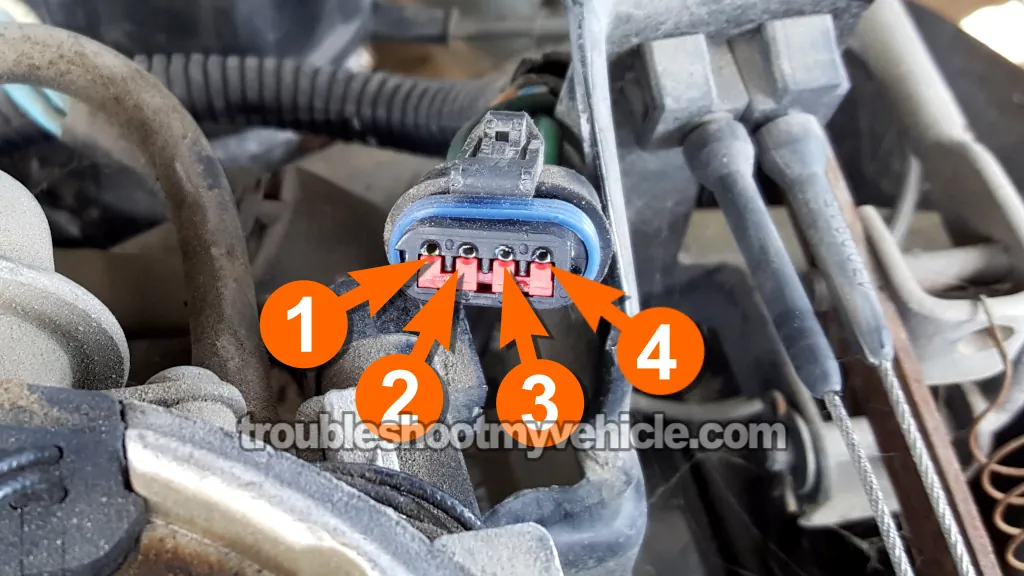
NOTE: Only run this test if both injectors failed to spray fuel in TEST 1.
If you've made it here, then you've already confirmed two things:
- TEST 1: Neither injector is spraying any fuel.
- TEST 2: Both injectors are getting 10 to 12 Volts of power.
Now in this section, we're gonna check whether the injectors are getting their activation signal —and we're gonna do it using an LED test light.
From my experience, using an LED is the easiest and safest way to check for those fuel injector pulse signals without risking damage to the fuel injection computer.
If you don't have an LED light, you can see what one looks like and you can also buy it here: Oznium Flush Mount 12V LED Light (at: amazon.com).
NOTE: Don't use a standard 12V test light for this check. A regular test light can overload the injector driver inside the fuel injection computer and damage it.
Alright, here's how to do the test:
- 1
Unplug the 4-wire connector from the fuel injectors. See the photo above to ID it.
- 2
Hook the red lead of your LED test light to terminal 1 on the connector.
NOTE: Double-check that this terminal connects to one of the dark green with black stripe (DK GRN/BLK) wires —that's a power wire. - 3
Now connect the black lead of the LED to terminal 2.
Terminal 2 should correspond to the tan (TAN) wire, which delivers the activation signal for injector #2. - 4
Have your helper crank the engine.
CAUTION: Keep your hands, tools, and wiring clear of anything that moves while the engine cranks. - 5
Watch for the LED to blink ON and OFF as the engine cranks.
- 6
Now disconnect the red LED lead from terminal 2.
- 7
Move the red lead to terminal 3.
Terminal 3 should connect to the white with dark blue stripe (WHT/DK BLU) wire —this one controls injector #1. - 8
Again, have your helper crank the engine.
CAUTION: Make sure you stay clear of moving parts during this step too. - 9
The LED should blink ON and OFF as the engine cranks.
Let's interpret your results:
CASE 1: The LED blinked ON and OFF on both signal wires. That's exactly what you want —it means the fuel injection computer is trying to fire both injectors.
If you've already confirmed all of the following:
- Both injectors aren't spraying (TEST 1).
- They're both getting proper voltage (TEST 2).
- They're receiving a firing signal from the computer (this test).
Then you've got two bad injectors if the fuel pump pressure is at 14.5 PSI. Time to replace them.
If you haven't checked the fuel pump's pressure, this tutorial will help you:
CASE 2: The LED did NOT blink on either signal wire. That tells you the injectors aren't being activated.
If you've already confirmed they have power (from TEST 2), the most likely issue is a break or open in the wiring between the injectors and the fuel injection computer.
Next step: test the wiring for continuity between the injector plug and the computer connector.
CASE 3: The LED blinked on only one of the signal wires. That usually means the other one isn't getting its signal because of a wiring issue between the fuel injector and the computer —assuming it's getting power (TEST 2).
Next step —check the wiring for continuity between the fuel injector connector and the fuel injection computer.
TEST 5: Making Sure The Fuel Injector Is Getting Power
NOTE: This test applies only if one injector is spraying fuel and the other isn't.
Since one injector is working, that tells us the ASD relay and the distributor pickup coil are both doing their job.
We also know that the working injector is getting voltage. What we need to figure out now is whether the injector that's not spraying is getting power too.
Here's how to run the test:
- 1
Unplug the 4-wire connector from the fuel injectors.
- 2
Connect your multimeter's black lead to the negative (-) battery terminal.
- 3
Set the multimeter to DC Volts mode.
- 4
Use the red lead to probe terminal 1 of the connector.
Make sure it's connected to one of the dark green with black stripe (DK GRN/BLK) wires. - 5
Have your helper turn the key to the ON position (don't crank the engine).
- 6
You should see a reading between 10 and 12 Volts for about 3 seconds.
This is the key on, engine off (KOEO) part of the test.
If the engine doesn't get cranked, the computer cuts power after a few seconds —that's normal. - 7
Now, have your helper crank the engine.
CAUTION: Keep your hands and tools clear of any moving parts during cranking. - 8
You should see 10 to 12 Volts the whole time the engine is cranking.
This part is the key on, engine running (KOER) test. - 9
Repeat this same voltage check on terminal 4.
NOTE: Make sure terminal 4 connects to the other DK GRN/BLK wire.
Here's how to read what your multimeter tells you:
CASE 1: You've got 10 to 12 Volts on both terminals during KOEO and KOER. That's the result we're hoping for.
Now that we know the non-spraying injector is getting power, it's time to find out if it's also receiving a firing signal. Go to: TEST 6: Making Sure The Fuel Injector Is Getting An Activation Signal.
CASE 2: One terminal shows no voltage in both KOEO and KOER. That means the non-working injector isn't getting power —but the other one is.
The most likely reason is a break in the wiring between that injector and the engine harness. Troubleshooting that kind of open-circuit issue is outside the scope of this guide, but you'll need to track it down and fix the break to restore power to that injector.