PART 2: Checking The Fuel Injector Spray Pattern
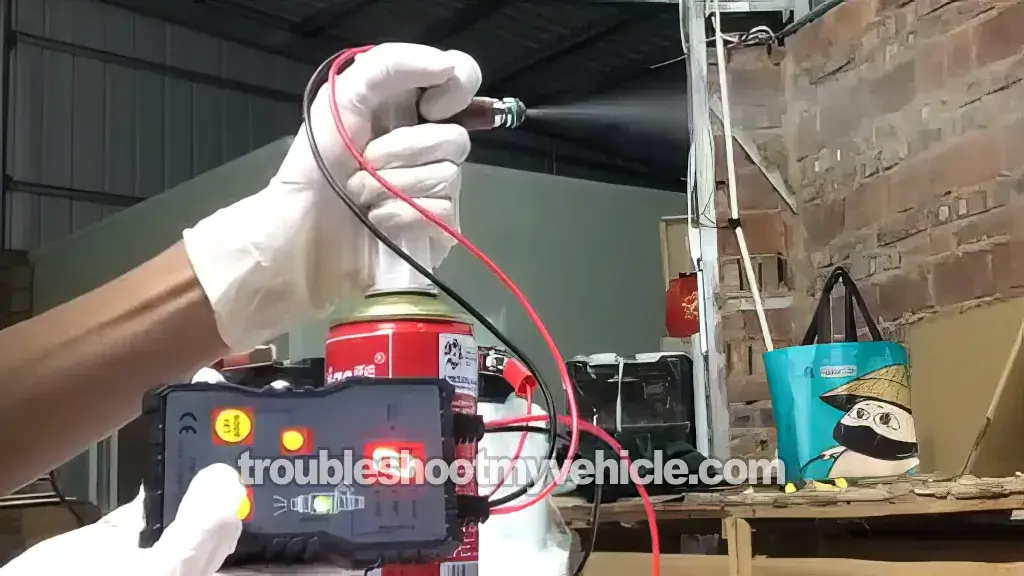
Now that you've ruled out any internal electrical issues with the fuel injector (by confirming its internal resistance is within specification), the next step is to remove it from the fuel injector rail.
After you've removed it from the fuel injector rail, you'll check that it can spray properly by using a DIY fuel injector cleaning tool (which you can buy online) and a can of brake cleaner.
This fuel injector cleaning tool kit includes two important components:
- A 12 Volt power module that triggers the fuel injector in pulses, similar to how the fuel injection computer does it.
- An adapter that connects the fuel injector to a spray can of brake cleaner.
Once you've set up the test, the fuel fuel injector you're testing should spray the brake cleaner in a fine mist. If the injector is clogged or has any type of internal issue, it'll either squirt the cleaner or fail to spray at all.
The awesome part about this fuel injector cleaning kit is that it doesn't cost much. You can purchase it here:
- QX Fuel Injector Tester & Adapter for Diagnosis and Cleaning of Injectors DIY Cleaning Tool Kit (at: amazon.com)
- EM276SET Fuel Injector Tester & Adapter DIY Cleaning Tool Kit Set (at: amazon.com)
IMPORTANT: Before installing the same or new fuel injector back on the fuel injector rail, take a look at: Important Tips For Installing A Fuel Injector.
CAUTION: Use safety glasses when performing the fuel injector cleaning procedure.
Alright, these are the test steps:
- 1
Remove the fuel injector.
- 2
Connect the fuel injector to the plastic adapter.
NOTE: I've found that securing the fuel injector to the adapter with a thick rubber band helps to make the whole process easier and less messier. - 3
Connect the fuel injector to the tool's power module.
NOTE: Follow the tool's safety and recommended set-up instructions. - 4
Connect the cleaning kit's power module to your pickup's battery.
- 5
Connect the fuel injector/adapter to a spray can of brake cleaner and press them onto the spray can.
- 6
Activate the power module.
- 7
The fuel injector should spray fuel in a fine mist and in a conical shape.
Let's interpret your test result:
CASE 1: The fuel injector did not spray at all. This tells you that the fuel injector is bad and needs to be replaced.
CASE 2: The fuel injector sprayed the brake cleaner in a fine mist and in a conical pattern. This tells you that the fuel injector is OK.
CASE 3: The fuel injector sprayed the brake cleaner in a squirt or a stream (not in a fine mist). This tells you that the fuel injector is dirty/clogged.
Continue cleaning the fuel injector until it starts to spray in a fine mist. If the cleaning it doesn't restore the injector's spray pattern to that of a fine mist, you'll need to replace it.
Important Tips For Installing A Fuel Injector
When you're done with your tests and installing either the same or a new fuel injector back on the fuel injector rail, it's important to follow these tips:
- Use New Fuel Injector O-Rings: Always replace the O-rings when installing a fuel injector, whether it's new or the same old one. New injectors usually come with new O-rings, but if you're reinstalling the same injector, you'll need to buy them separately. I really want to emphasize that new O-rings are super important for ensuring a good seal and avoiding gasoline and vacuum leaks.
- Lubricate The O-Rings: It's important to coat the O-rings with a thin layer of clean engine oil (5W-30 or lighter). Don't use any silicone-based grease or other types of lubricants (like wheel bearing grease).
Lubricating the O-rings with light engine oil helps avoid damaging them when inserting the fuel injector into both the injector rail and the intake manifold port. If installed without lubrication, they'll end up getting damaged and you'll have gasoline or vacuum leaks when you crank and start the engine. - Replace Broken Connectors: Ford fuel injector connectors are known for their locking tabs breaking when disconnected from the fuel injector. If the fuel injector connector is damaged, you've go to replace it now that you've got the plenum removed and have easy access to it.
- Avoid Using Butt Connectors: Avoid using butt connectors like the plague to join the new connector's wires to the engine wiring harness. Instead, solder the wires for a long-lasting repair. Butt connectors will lose their grip on the wires over time, leading to false contact issues.
Remember, the goal is to prevent gasoline leaks and avoid the risk of fire. Take your time to ensure everything is properly seated and secure.
Precautions To Take When Removing The Intake Manifold Plenum
Before and during the intake manifold's plenum removal, keep the following important tips in mind:
- Have A Repair Manual On Hand: Removing the intake manifold plenum isn't too complicated, but it does involve removing quite a few components. This is where a repair manual (preferably a Haynes Repair Manual, as I find Chilton manuals less reliable) will save the day by explaining the process in detail. The manual will also provide torque specifications for the bolts.
- Disconnect The Battery: Disconnect the negative (-) battery cable before removing the intake manifold plenum and keep it disconnected throughout the fuel injector testing procedure.
- Prevent Foreign Objects From Falling Into The Open Intake Manifold Ports: You've got to be careful that no foreign objects, such as bolts, nuts, or any metal parts, fall into the open manifold port runners. Once the plenum is removed, cover the open intake runners with a clean rag or rags to prevent anything from falling in.
- Keep Removed Parts Away From Engine Compartment: As you remove bolts, nuts, and other components from the intake plenum, place them in a container and keep them away from the engine compartment.
- Do Not Crank The Engine: Never crank the engine with the plenum removed from the lower intake manifold.
Any metal part falls into the open intake runners, without you knowing, and the engine is started, you're gonna be in a big world of hurt! In about 99% of the cases, you'll need to remove the cylinder head to retrieve the part that fell in (and fix the damage). So be alert and be careful.
Don't stress about this -taking off the plenum isn't rocket science; lots of folks get it done without any problems. The key is to take some simple precautions to avoid any complications or issues.
More 4.2L Ford E150 And E250 Test Tutorials
If this tutorial was helpful, be sure and take a look at all of the 4.2L V6 E150 and E250 diagnostic tutorials and wiring diagrams in this index:
Here's a sample of the tutorials you'll find there:
- How To Test The Throttle Position Sensor (1997-2000 4.2L V6 Ford E150, E250).
- How To Test Engine Compression (1997-2003 4.2L V6 Ford E150, E250).
- How To Test The Fuel Pump (1997-2000 4.2L V6 Ford E150, E250).
- How To Test The CKP Sensor With A Multimeter (1997-2003 4.2L V6 Ford E150, E250).
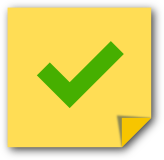
If this info saved the day, buy me a beer!
