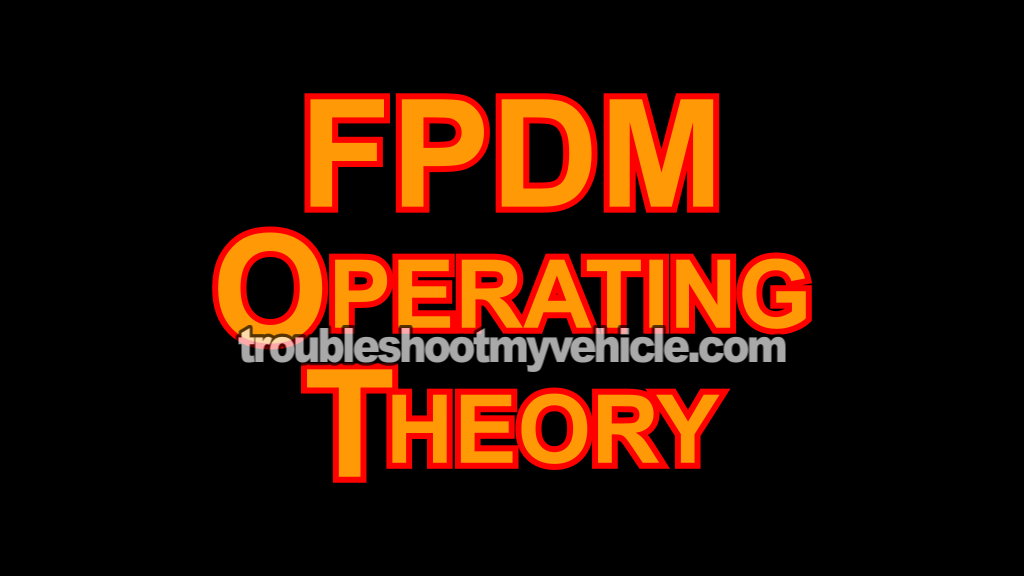
This tutorial is a full breakdown —a comprehensive primer— on how the FPDM, PCM, fuel pump, and related signals all work together to control fuel delivery on your 2004–2010 4.0L V6 Ford Explorer or Mercury Mountaineer.
I'm gonna walk through how the system operates under normal conditions, what each signal means, and how everything ties back to fuel pressure control.
Once you understand how it's supposed to work, you'll be in a much better position to diagnose what's wrong when it doesn't.
Contents of this tutorial:
- What Does the Fuel Pump Driver Module Do?
- Fuel Pump Output Control Basics.
- Fuel Pump Control (FPC) Signal Essentials.
- Fuel Pump Ground (FP RTN) Signal Essentials.
- Fuel Pump Monitor (FPM) Signal Essentials.
- Fuel Rail Pressure (FRP) Sensor.
- More Fuel Pump Troubleshooting Help.
- More 4.0L V6 Ford Explorer And Mercury Mountaineer Tutorials.
APPLIES TO: This tutorial applies to the following vehicles:
- 4.0L V6 Ford Explorer: 2004, 2005, 2006, 2007, 2008, 2009, 2010.
- 4.0L V6 Mercury Mountaineer: 2004, 2005, 2006, 2007, 2008, 2009, 2010.
MORE FUEL PUMP DIAGNOSTIC RESOURCES: You can find fuel pump circuit wiring diagrams, related fuel pump tests, and the inertia switch tests in this section:
FUEL PUMP DRIVER MODULE (FPDM) TESTS: This tutorial is a step-by-step guide on how to test the FPDM itself:
What Does the Fuel Pump Driver Module Do?
To really understand the important role that the fuel pump driver module plays in the returnless fuel system of your 2004–2010 4.0L V6 Ford Explorer (or Mercury Mountaineer), we need to first look at the older style fuel system —one that uses a mechanical fuel pressure regulator and a return line to send excess fuel and pressure back to the tank.
In these older systems:
- The fuel pump relay provides power to the fuel pump as long as the engine is cranking or running.
- Ground is always present at the fuel pump.
- The pump runs at full speed all the time, delivering maximum pressure output.
- A mechanical fuel pressure regulator —mounted on the injector rail— bleeds off any excess pressure and returns it to the tank.
- A return fuel line carries that excess pressure/fuel back to the tank.
Maintaining fuel pressure mechanically was a super simple design that worked almost flawlessly for decades! Too bad for you and me that the patents expired and the cash cow this system provided dried up.
This modern system is a far cry from the simplicity of the older setup. Your Ford's returnless fuel system uses a fuel pump driver module (FPDM), and unlike the old-school design, there's no return line sending excess fuel back to the tank.
In this newer setup:
- The fuel pump relay supplies power to the FPDM module (not directly to the fuel pump) as long as the engine is cranking or running (key in RUN or START).
- Ground is supplied by the fuel pump driver module (FPDM)—not directly to the pump.
- But this Ground isn't static —it's pulse width modulated (PWM) to precisely control fuel pressure.
- The FPDM varies the strength of the Ground anywhere from 10% to 100%, depending on what the PCM wants in terms of fuel pressure.
- The fuel pump doesn't run at full blast all the time —it only puts out the pressure the PCM is asking for.
- There's an electronic fuel pressure sensor mounted on the injector rail that constantly reports back to the PCM. Based on this feedback, the PCM tells the FPDM to ramp the fuel pump up, down, or completely off.
- Since the system is regulated electronically in real-time, there's no need for a mechanical regulator or a return line —there's never "extra" pressure to bleed off.
Of course, with more electronics and more control comes more complexity —and more things that can go wrong. And when they do, well... That's where the repair bills start climbing. In my opinion, this system wasn't just designed for efficiency —it also helps keep the money flowing into the auto repair economy.
Fuel Pump Output Control Basics

So now that you know the Fuel Pump Driver Module (also called the fuel pump control module) acts as the middleman between the PCM and the fuel pump —translating the PCM's fuel delivery commands into real-world fuel pump activity— let's break down the different signals involved in its operation:
- FPDM PWR signal: When you turn the key and crank the engine, the fuel pump relay activates and sends battery voltage to the fuel pump inertia switch. If the switch hasn't been tripped, those 12 Volts get passed along to the fuel pump driver module.
- PWR GND signal: Chassis Ground is available to the FPDM at all times through its dedicated Ground wire.
- Fuel Pump Control (FPC) signal: This signal comes from the PCM and is a duty cycle (%) signal that tells the FPDM how fast (or slow) the pump should run:
- The higher the duty cycle percentage, the more fuel the PCM is asking for.
- The lower the duty cycle percentage, the less fuel is needed.
- FP PWR signal: This is the 12 Volt power supply the FPDM sends to the fuel pump after receiving the FPC signal from the PCM.
- FP RTN signal: This is the modulated Ground signal the FPDM sends to the fuel pump. It pulses the Ground ON and OFF rapidly (PWM style) to control how much current reaches the pump.
- The faster the pulse rate, the more current the pump gets —which increases fuel pressure.
- The slower the pulse rate, the less current the pump gets —which lowers fuel pressure.
- Fuel Pump Monitor (FPM) signal: This is a feedback signal sent back to the PCM by the FPDM. It's also duty-cycle based and reports what's actually happening in the fuel pump circuit —and inside the FPDM. More on this one in: Fuel Pump Monitor (FPM) Signal Essentials
Let's keep going. These upcoming sections will break down the specifics of the FP RTN, FPC, and FPM signals —and they'll give you the insight you need to troubleshoot fuel pump and FPDM issues with confidence.
Fuel Pump Control (FPC) Signal Essentials
The most important thing to know about the fuel pump control (FPC) signal is this: the fuel pump driver module (FPDM) is programmed to recognize only certain duty cycle percentages as valid commands.
If the FPC signal falls outside this programmed range, the FPDM considers the signal invalid —and when that happens, the fuel pump won't turn on, resulting in an engine no-start.
So in this section, I want to explain what the FPDM considers a valid signal. This knowledge will help you when you're testing the FPC signal with your multimeter.
Here's the breakdown: the FPDM is programmed to recognize a duty cycle between 5% and 50% as a valid "ON" command from the PCM to activate the fuel pump.
As I mentioned earlier:
- The lower the duty cycle (closer to 5%), the FPDM interprets that as the PCM requesting lower fuel pressure.
- The higher the duty cycle (closer to 50%), the FPDM interprets that as the PCM wanting higher fuel pressure.
- At 50% duty cycle, the FPDM knows the PCM is asking for maximum fuel pump output —full pressure.
The other valid range is when the PCM wants the fuel pump turned off. In that case, the FPC signal will be between 70% and 80% duty cycle.
Any duty cycle percentage outside of these two ranges means the FPDM won't respond —and you'll end up with an engine that won't start.
NOTE: The FPC duty cycle signal is directly related to how much Ground the fuel pump driver module applies to the fuel pump. I'll explain this in more detail in the section Fuel Pump Ground (FP RTN) Signal Essentials.
Fuel Pump Ground (FP RTN) Signal Essentials
In the previous section, I mentioned that the Fuel Pump Control (FPC) signal is tied directly to the amount of Ground the fuel pump driver module (FPDM) applies to the fuel pump. As you know by now, the lower the duty cycle of the FPC signal, the less fuel pressure the PCM is requesting. The higher the duty cycle, the more pressure it wants.
Ford was kind enough to give us a simple formula to work with:
- FPC duty cycle × 2 = % of full Ground applied to the fuel pump.
In other words, the FPDM takes the FPC duty cycle signal, doubles it, and uses that result to determine how much Pulse Width Modulated (PWM) Ground to apply to the pump. That's how it controls pump speed and pressure output.
Here are a few examples to make this crystal clear:
- FPC = 50% → 50 × 2 = 100 → The FPDM applies 100% Ground → Fuel pump spins at full speed and outputs max pressure.
- FPC = 40% → 40 × 2 = 80 → The FPDM applies 80% Ground → Fuel pump spins slower and produces less pressure.
- FPC = 25% → 25 × 2 = 50 → The FPDM applies 50% Ground → Fuel pump speed and pressure are reduced even further.
Simple math, but it gives you a powerful window into what's going on inside the system while you're testing it. The multimeter shows the FPC duty cycle —you do the math, and you know exactly how much work the fuel pump is being asked to do.
Fuel Pump Monitor (FPM) Signal Essentials
The last signal, we're gonna cover is the Fuel Pump Monitor (FPM) signal, which serves as a feedback line from the fuel pump driver module (FPDM) back to the PCM.
The FPDM sends the FPM signal to let the PCM know what's actually going on in the circuit after the PCM sends out its Fuel Pump Control (FPC) signal and the FPDM does its little song and dance with the fuel pump.
Now, don't expect a ton of detail from this signal. It's not reporting exact pressures or voltages. It's more like a basic status report, and it comes in three flavors —each one represented by a specific duty cycle:
- 50% duty cycle: Everything is working correctly. The FPDM got a valid FPC signal and it's doing its job without issue.
- The fuel pump could be bad, but if the FPDM itself is OK and doing its job, it'll still send a 50% duty cycle signal.
- 25% duty cycle: The FPDM didn't receive a valid FPC signal —or it didn't receive one at all.
- 75% duty cycle: The FPDM detected a fault in the fuel pump circuit, such as an open wire, a short, or an overcurrent condition (like a dying fuel pump drawing too much juice).
This feedback loop is how the PCM keeps tabs on what's happening downstream. If the FPM signal doesn't match what the PCM expects, you'll either get a trouble code or a fuel delivery issue —or both.
Fuel Rail Pressure (FRP) Sensor
There's one more key player in this fuel control loop: the Fuel Rail Pressure (FRP) sensor. This sensor acts as the "eyes" of the PCM —it constantly reports the actual fuel pressure at the fuel injector rail.
The PCM uses this live data to determine how much fuel the engine needs based on load and driving conditions. Then it adjusts the FPC signal duty cycle sent to the FPDM to dial in fuel pump output in real time.
This constant feedback loop ensures:
- Optimal engine performance under all load conditions.
- Maximum fuel economy by avoiding unnecessary pump output.
- Lower emissions by keeping pressure precisely regulated.
Working together with the FPM feedback signal from the FPDM, the PCM is able to both control the fuel system And monitor its health.
If something's off —like the FPM signal doesn't match expectations or the FRP sensor reports inconsistent pressure— you'll likely get a diagnostic trouble code, such as P1233, P1235, or P1237. In some cases, the PCM may shut down the fuel pump entirely as a safety measure.
More Fuel Pump Troubleshooting Help
FUEL PUMP PRESSURE TESTS:
FUEL PUMP DRIVER MODULE (FPDM) TESTS:
- Fuel Pump Driver Module Tests (2004-2010 4.0L V6 Ford Explorer And Mercury Mountaineer).
- Bypassing The FPDM Module (2004-2010 4.0L V6 Ford Explorer And Mercury Mountaineer).
FUEL PUMP INERTIA SWITCH TESTS:
- Fuel Pump Inertia Switch Tests (1991-2010 4.0L V6 Ford Explorer, Aerostar, And Mercury Mountaineer).
- Power To Fuel Pump Check (1991-2010 4.0L V6 Ford Explorer, Aerostar, And Mercury Mountaineer).
ENGINE NO-START DIAGNOSTICS:
FUEL PUMP CIRCUIT DIAGRAMS:
- Fuel Pump Circuit Wiring Diagram (2004 4.0L V6 Ford Explorer And Mercury Mountaineer).
- Fuel Pump Circuit Wiring Diagram (2005 4.0L V6 Ford Explorer And Mercury Mountaineer).
- Fuel Pump Circuit Wiring Diagram (2006-2010 4.0L V6 Ford Explorer And Mercury Mountaineer).
More 4.0L V6 Ford Explorer And Mercury Mountaineer Tutorials
I have written several more 4.0L V6 Explorer/Mountaineer specific test articles. You can find them all here:
The following tutorials are a sample of the articles you'll find in the index:
- How To Test The CKP Sensor (1997-2010 4.0L V6 Ford Explorer And Mercury Mountaineer).
- Fuel Pressure Specifications (1991-2010 4.0L V6 Ford Explorer, Mercury Mountaineer).
- How To Test For A Blown Head Gasket (1991-2010 4.0L V6 Ford Explorer, Aerostar, And Mercury Mountaineer).
- Troubleshooting P0171 And P0174 (1996-2003 4.0L V6 Ford Explorer, Aerostar, And Mercury Mountaineer).
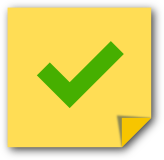
If this info saved the day, buy me a beer!
